Could you scuba dive in space?
We get a lot of questions about our technology here at EOI Space; turns out when you are flying into largely unchartered territory people are skeptical and have questions. One of the most common questions is “How can you stay at 250km, you must be using air breathing technology, right?” Typically, our answer is “of course we are air breathing; but like a scuba diver we can carry all the oxygen (in our case krypton) we need in two tanks.” Air breathing is a complex problem with a unique solution space. Here at EOI Space we were determined that we could meet our mission specs with on-board propellant. In fact, we determined air breathing was not well suited to our mission specs due to some of its constraints and requirements. In this post we will take you through that evaluation process and share some of the latest testing results we are getting with our patented HET-X thruster design.
Flying very low is a systems problem and we wanted a system designed from the ground up for flying in VLEO. So, we started with mission requirements:
- A low-profile bus to minimize drag
- An optical payload capable of producing 15cm Pan, R, G, B, & NIR data from 300km
- The agility to do persistent imaging and quickly move between Nadir and 70 off-Nadir angle (ONA) for imaging
- Keep the build cost as low as possible to ensure a space vehicle at a price point that support resilient launch supply
- Maintain a 250km orbit for 5 years with enough extra propulsion to support orbit transfers, margin, and response to unusual solar activity.
At altitudes between 250-300km the increase in drag from standard LEO altitudes is immense and increases quickly as you descend. The drag on our Stingray bus design is ~0.3 mN at 300km and increases to ~1.5 mN at 250km. With all this in mind we set out to see what was possible with our team’s long history of experience with electric propulsion systems.
In our previous post we introduced you to the HET-X thruster that EOI Space has built. There we shared some of the early research and design that went into our HET-X thruster which operates at moderate-to-high operating power, has a small form factor, and is designed to operate on various propellants. HET-X brings several advantages over traditional systems:
- The system design takes advantage of high efficiency HET technology and modern power technology to provide more thrust, more efficiently, that is applied at the most convenient and efficient points in orbit.
- It is capable of operation up to about 4000 watts and higher power HETs are more efficient (by about 10% in EOI Space’s case).
- Enables more efficient impulsive maneuvers (increases overall efficiency by about 15%).
- Shorter impulsive maneuvers reduce lifetime concerns (Our planned five-year mission only requires about 2000 hours of operation, much less than typical HET lifetime).
What does all this mean? Well, for starters we have a system with some very desirable features that only needs onboard propellant to meet mission requirements. To operate at 250km for 5 years (again this is enough extra propulsion to support orbit transfers, margin, and response to unusual solar activity) we are at <10% mass fraction. This is very reasonable and our ability to use different noble gases means we can manage cost easily against market fluctuations. With all this in mind we set out to build and test the HET-X system. We have done extensive testing and are now on our sixth generation of the design which is in the final weeks of testing at the University of Washington (UW).
The intent of ground test goes far beyond determining thruster performance. Ground test also teaches us how to program the propulsion system on the Stingray. There are a large number of parameters that must be set to operate a Hall Effect Thruster, such as discharge voltage, propellant flow rate, magnet currents, and so on. We test over a wide range of parameters on the ground to find the best regions in parameter space. These regions include which parameter values give the highest propellant efficiency, quantified as Isp, and which parameters give us the highest thrust for a given power input. Exploring HET-X parameter space thoroughly on the ground simplifies operation in orbit, because ground test has already identified the best HET-X parameter combinations.We will soon be moving to University of Washington’s Space Propulsion and Advanced Concepts Engineering (SPACE) Lab’s new larger vacuum chamber. Currently we are limited in fully testing the performance of our design due to the limited by pumping speed of current chamber.
Once we are in the larger chamber, we will perform a full exploration of parameter space to find most effective operating parameters and start/stop procedures:
- This implements UW SPACE machine learning techniques.
- A fully automated test-as-we-fly approach.
- Test operation up to 4kW possible, higher than expected power for highest efficiency at 450 V, 2300s Isp.
During this stage we will identify life limiters, if any. Then we will develop a propulsion model for our flight software team to implement (allowing optimization in flight of operating parameters such as length of burn, discharge potential, propellant flow rate, and so on).
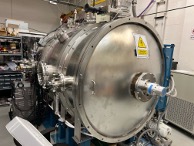
And we’ll finish with some of the current test results. Our HET-X performance is already sufficiently good for the Stingray mission. The plots shown below, for 1.0kW operation, are a preview of the type of measurements to be made in the larger chamber. A single data point at 300V and 1.5kW indicated a large improvement in Isp and efficiency. We now believe we have a unique and robust electric propulsion system that gives us more flexibility in how we operate and an exceptional mission life with only onboard propellant. Air breathing has its own unique pros and cons and make it ideal for certain missions, but not for the Stingray mission.
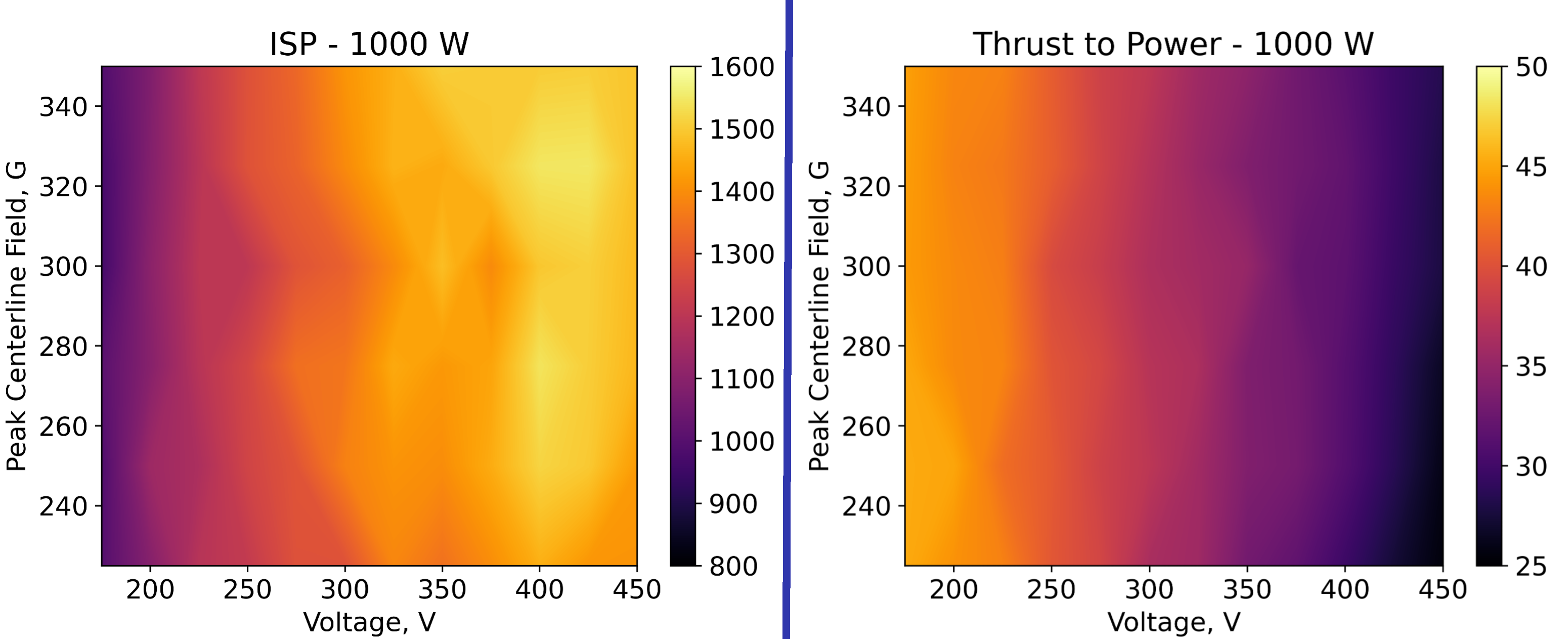
In conclusion space is hard and VLEO is no exception. Air breathing has shown some great strides and promise for certain missions in the future, and we are still seeing advances in electric propulsion like those we have advanced with HET-X. EOI now has a robust and tested design for a unique system that takes advantage of advanced power and propulsion technologies that are available now. This system can operate in low and higher power modes that extend the capability of conventional in-space propulsion systems. As we have shown in our research, design, and extensive testing the HET-X system is uniquely positioned to support the Stingray mission. This allows us to keep our satellite flexible and ready for change in this very-low altitude, provide a five-year lifetime, and keep our build and launch costs very reasonable. We believe that dynamic satellites like the Stingray will be great contributors to a more resilient earth observation capability in space and keeping costs down is a key driver of that goal.
More to come as we continue development and testing this fall. Follow us on our blog site and on LinkedIn LinkedIn.
Contact us at info@eoi.space or through the contact form on our website.
