Rethinking Optics for Enhanced Earth Observation
We are excited to share some early details on the Optical Payload for our first Stingray satellite. At EOI Space our founders set out to build a novel space vehicle designed from first principles for flying at <=300km above the earth. Flying at such a low altitude introduces a few key complications, which we will discuss later, that render typical optical payload designs sub-optimal for use in VLEO. Upon completion of the VLEO-optimized bus design, it was realized that the Stingray would benefit from a custom optical payload. So off to the drawing board the team went again and partnered with our good friends at Seattle Photonics to create a new optical payload for VLEO.
In VLEO, atmospheric drag is a significant factor to contend with when it comes to spacecraft design. The Stingray bus design is in part focused on reducing the front cross sectional area of the satellite exposed to the atmosphere to reduce drag. In order to fit a traditional optical design into the Stingray, this would have required using a very small focal length optic, or an optic looking out the aft end of the satellite; neither of which were desirable design choices. In LEO, atmospheric drag is much less of a concern, therefore there are fewer constraints on the shape of the satellite. Typical LEO satellites have a large optic continually pointed down at the earth as it travels. However, this means you have a large cross section of the satellite pointing in the direction of travel. You can see this depicted in the image below.
By reducing the spacecraft’s cross-section, and thereby reducing the effects of drag, this means EOI’s Stingray can use fuel efficiently, fly longer missions, and ultimately provide more of its high-quality images to our customers. EOI’s solution offers the best of both worlds: imagery whose quality and resolution matches that of traditional optical payloads, and a long operational lifetime.
A great deal of R&D went into designing a first gen optic and then learning from that design to ultimately arrive at our current optical payload architecture. As the super structure arrived at our facility late last year, we thought this was a great time to start talking about it.
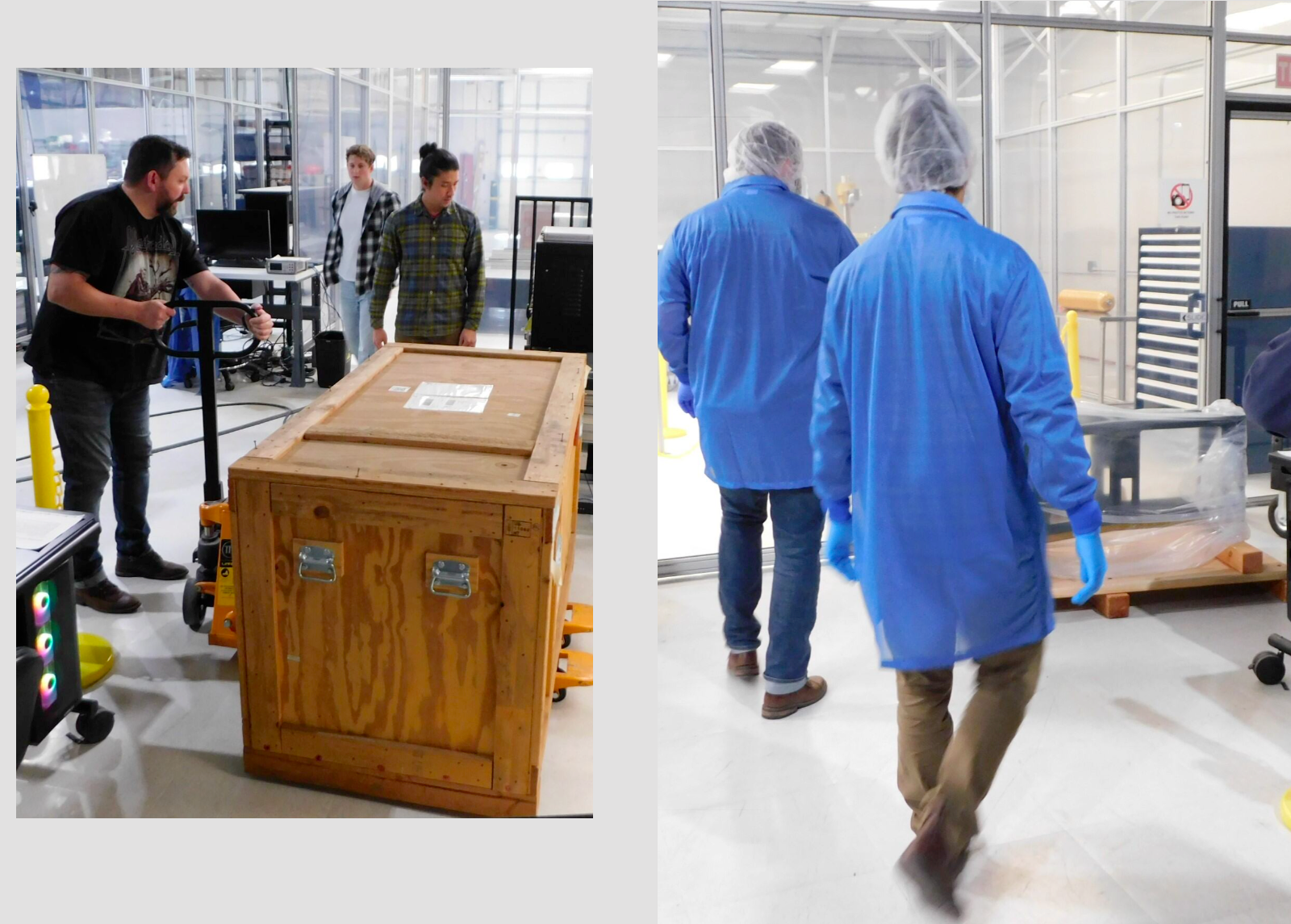
After finalizing the design for our optical payload the team at Rock West Composites manufactured the super structure out of carbon composites for us and shipped it to our facility in Louisville, CO last year. We moved it into our clean room and unboxed it in November of 2024. Meanwhile the lens cell design is currently going through environmental testing offsite. The team is excited to be getting these components finalized so we can start assembling the full optical payload soon.
We had two goals in our design to achieve frequent and very high-resolution imaging:
- A focal length greater than 2m
- An imager that was always looking down
To achieve this, we went with an optic that includes a fold mirror, this design allows
- an optical payload that is always looking down, while keeping the spacecraft flying in the position of least atmospheric drag
- a focal length greater than 2m
- a primary optic >40cm
This results in our ability to deliver 15cm imagery from an altitude of 300km. As for how we achieve that across all bands (Pan, Red, Green, Blue, Near IR), you’ll have to wait for a future blog post on our camera system.
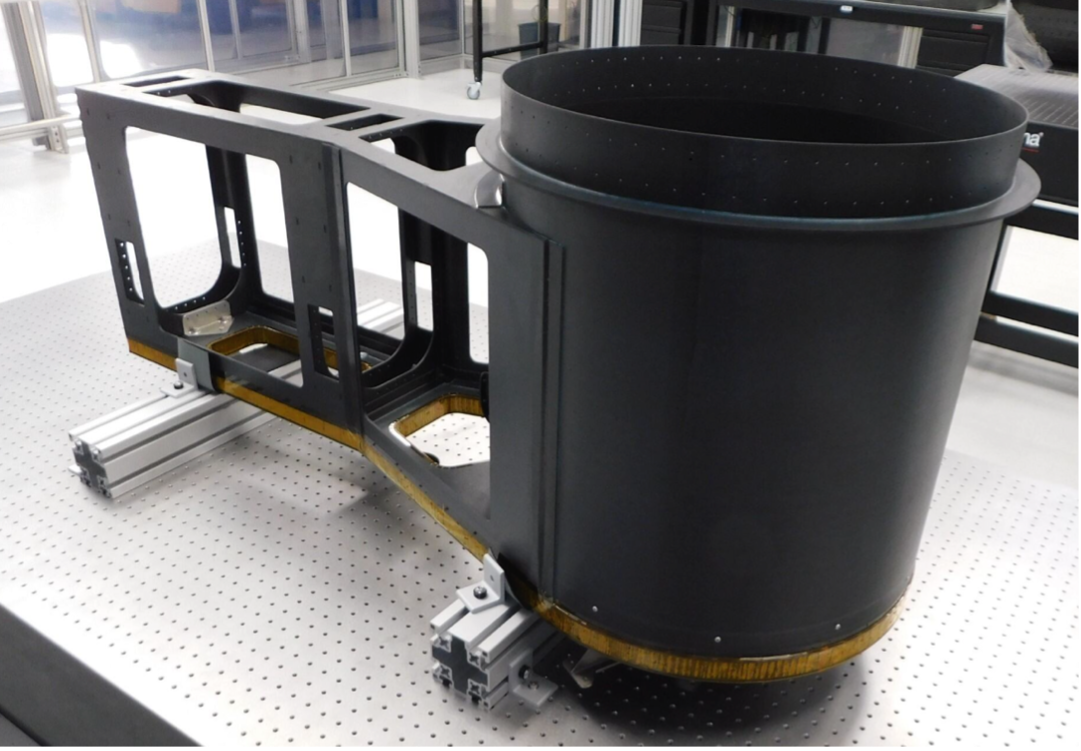
The team is currently focused on preparing the fixturing and equipment necessary to facilitate Assembly, Integration, and Testing (AI&T) of the optical payload. After many years of careful R&D and ensuring we have bought down as much risk in our designs as possible, we are thrilled to be starting to get down to work in the clean room. We’ll continue to share more on our unique optical payload throughout the year.
More to come as we continue development and testing this spring. Follow us on our blog site and on LinkedIn LinkedIn.
Contact us at info@eoi.space or through the contact form on our website.
